Case study: Tecnam France, aeronautical maintenance revolution thanks to Tracing Flight Solutions
(Reading 3 mn)
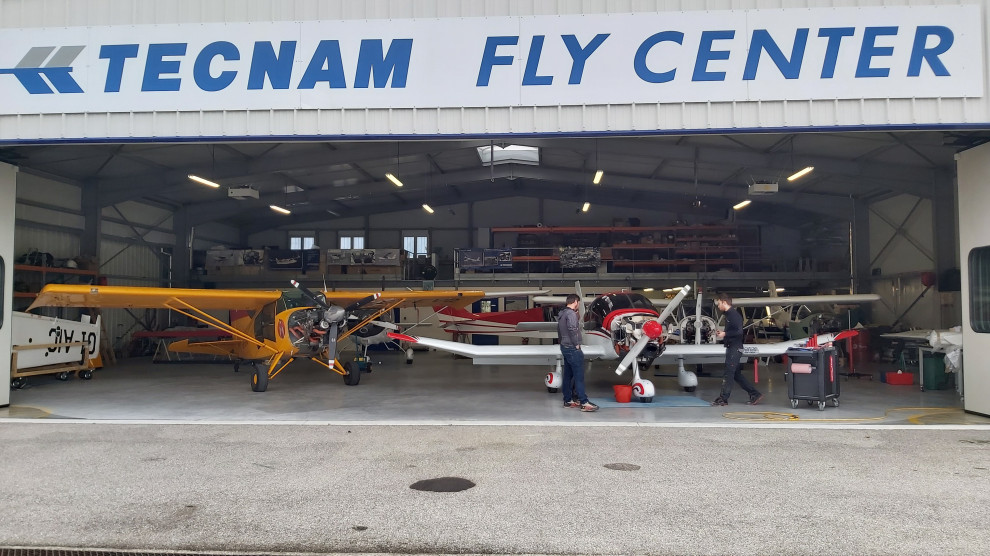
Context
Tecnam France, based at the Bellegrade Vouvray aerodrome (Ain 01), specializes in the exclusive sale of light aircraft and ultralights of the Tecnam type as well as in aeronautical maintenance.
In 2016, Justin J, a pilot with time-out, as he likes to say, and an experienced maintenance manager, takes over the Tecnam maintenance workshop, to manage a permanent and diversified fleet of 15 aircraft, plus passing aircraft and microlight.
With a staff of 2 mechanics, two clerical and one apprentice, the workshop obtained its Part CAO certification in August 2022, which marked a new stage in its development.
Challenges
Prior to the integration of Tracing Flight solutions, the workshop faced major challenges:
- Manual inventory management via Excel, source of many errors and loss of time. Justin called the previous solution “stale” resulting in large discrepancies between theoretical and actual stocks.
- Time-consuming processes, particularly in the management of Kardex and reports, which increased administrative burden as customer requests increased.
- Difficulties in monitoring and optimising administrative tasks, especially with regard to the traceability of parts and certificates of conformity.
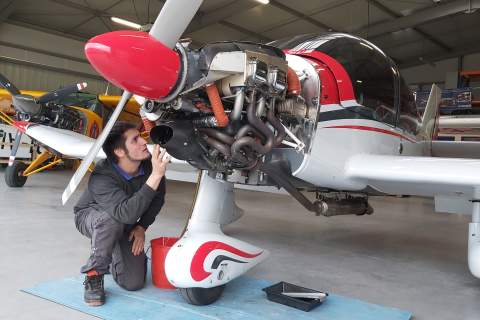
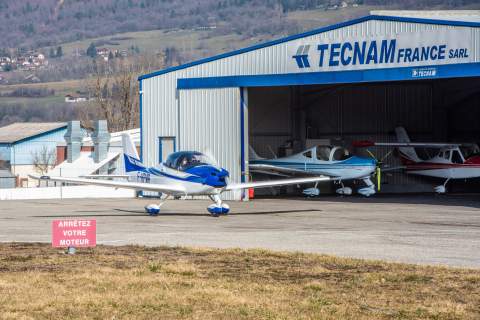
The Tracing Flight solution
After comparing different software options, in January 2018 Tecnam France chose Tracing Line, Tracing Gest and Tracing Nav to modernize its processes, a complete and modular solution for workshop management.
These tools have been gradually integrated to cover inventory management, Kardex, and aircraft maintenance. The system was not closed, it could evolve. We appreciated this flexibility and the regular updates allowed us to adapt the solution to our needs.”
Benefits and concrete results
The introduction of Tracing Flight has transformed workshop management and brought significant results:
- Improved inventory management:
Inventory management has been a revolution for Tecnam. "Before, it took a week to reconcile inventories. Today, two days is enough and the stock is accurate," says Justin. This optimization allowed the team to focus on higher value added tasks.
- Enhanced traceability and reporting:
"You can find the history of a part in seconds". With this complete traceability, audits are simplified and faster. The software allows for efficient tracking of work sheets and repair orders, facilitating team coordination.
- Time savings in maintenance and administration:
The team has successfully reduced by three times the time spent on administrative tasks by plane, freeing up more time for maintenance. "Paper printing has also decreased from 50% to 75%, and we are aiming for a 90% reduction through digital job cards."
- Flexibility and operational agility:
Even though some adjustments were needed at the start, Justin insists on the flexibility of the Tracing Flight solutions. "It was great because the system really adapts."
Conclusion
Thanks to the Tracing Flight solutions, Tecnam France not only modernized its workshop management but also optimized its processes, improved traceability which is described by Justin as “exceptional” and allowed the team to focus on its core business. The flexibility and scalability of the solution were decisive in adapting to Tecnam’s specific needs.
The final word
“Software solutions that I appreciate, and recommend. They have allowed us to reduce our administrative time by three and improve our interventions. Our customers feel it, and they come back happy!”